Common O-Ring Failures
Extrusion (Nibbling)

What is Extrusion (Nibbling)?
The seal develops ragged edges (generally on the low-pressure side) which appear tattered.
What are the causes of Extrusion? Conditions which contribute to failure are:
- Excessive clearances.
- Excessive pressure.
- Low modulus/hardness elastomer.
- Excessive gland fill.
- Irregular clearance gaps.
- Sharp gland edges.
- Improper sizing.
How to Correct Extrusion? Some suggestions are:
- Decrease clearances.
- Higher-modulus/hardness elastomer.
- Proper gland design.
- Use of polymer backup rings.
Over-Compression

What is Over-Compression?
The seal exhibits parallel flat surfaces (corresponding to the contact areas) and may develop circumferential splits within the flattened surfaces.
What causes Over- Compression? Condition such as:
- Improper design-failure to account for thermal or chemical volume changes,
- or excessive compression.
How to correct Over-Compression?
- Gland design should take into account material responses to chemical and thermal environments.
Spiral Failure
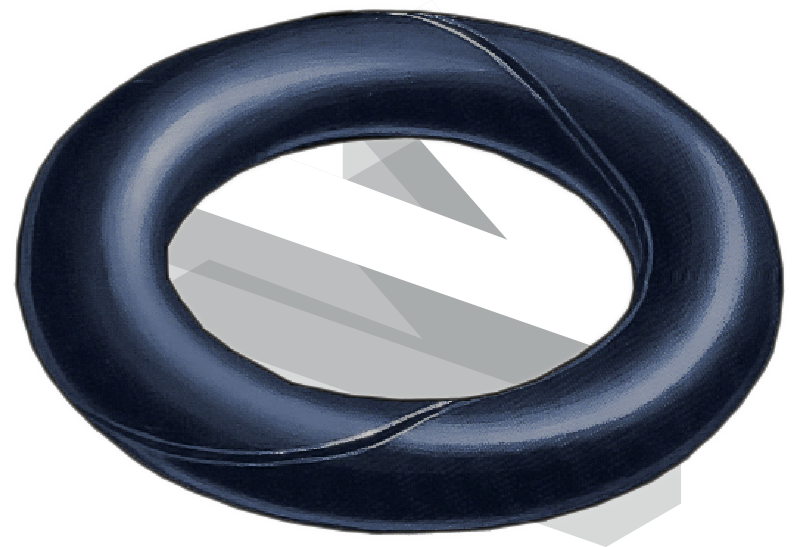
What is a Spiral Failure?
As the name implies, the seal will have spiral type cuts or marks going around it. Often found on long stroke hydraulic piston seals and to a lesser degree on rod seals.
What are the causes contributing to the Spiral Failure? Some of the conditions to cause the failure are:
- The O-Ring is not installed correctly or the installation is tight.
- The reciprocating speed is too slow. Low-modulus/hardness elastomer.
- Abnormal O-ring surface finish, including excessive dividing line.
- Excessive gland width.
- Gland surface finish is irregular or rough.
- Lubrication is inadequate
How to correct Spiral Failure? Some suggestions are:
- Correct installation procedures.
- Higher-modulus elastomers.
- Improve the internally lubed elastomers.
- Correct the gland design.
- Gland surface finish should be 8-16 microinch RMS.
- If possible use polymer backup rings.
Compression Set

What is Compression Set?
The O-Ring should be a continuous seal line between sealed surfaces. In the case of Compression Set, the seal shows as a flat sided cross section, the flat side corresponding to the matting seal surfaces.
What are the causes contributing to the Compression Set? Compression Set can be caused by any or a combination of the following:
- Excessive squeeze of the adjustable glands
- Excessive temperature causing the O-Ring to harden and lose its elasticity
- Incompletely cured elastomer during production
- Elastomer has too high a compression set.
- Volume swell due to system fluids
How to correct Compression Set? Some steps to take are:
- Lower the squeeze of the adjustable glands
- Reduce the operating temperature and check friction heat build up.
- Choose O-Ring material compatible with the task conditions
Outgassing/Extraction
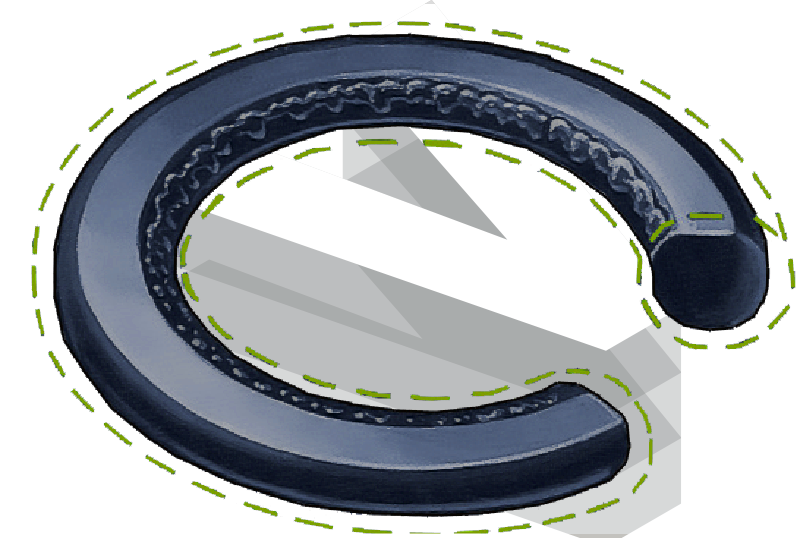
What is Outgassing/Extraction?
The failure is often very difficult to detect from examination of the seal. The seal may exhibit a decrease in cross-sectional size.
What causes Outgassing/Extraction? Factors such as:
- Improper or improperly cured elastomer.
- High vacuum levels.
- Low hardness/plasticized elastomer.
How to correct Outgassing/Extraction? Watch for:
- Avoid plasticized elastomers.
- Ensure all seals are properly post-cured to minimize outgassing.
Installation Damage

What is Installation Damage?
The seal or parts of the seal may exhibit small cuts, nicks, or gashes.
What causes Installation Damage? Possible causes are:
- Sharp edges on the glands or components.
- Improper sizing of elastomer.
- Low-modulus/hardness elastomer.
- Elastomer surface contamination.
How to correct Installation Damage? Consider:
- Remove all sharp edges.
- Proper gland design.
- Proper elastomer sizing.
- Higher-modulus/hardness elastomer.
Chemical Degradation

What is Chemical Degradation?
The seal may exhibit many signs of degradation including blisters, cracking, voids or discoloration. In some cases, the degradation is observable only by measurement of physical properties.
What causes Chemical Degradation? Condition such as:
- Incompatibility with the chemical and/or thermal environment.
How to correct Chemical Degradation?
- Selection of more chemically resistant elastomer.
Thermal Degradation

What is Thermal Degradation?
The seal may exhibit radial cracks located on the highest temperature surfaces. In addition, certain elastomers may exhibit signs of softening-a shiny surface as a result of excessive temperatures.
What causes Thermal Degradation? Condition such as:
- Elastomer thermal properties
- Excessive temperature excursions of cycling
How to correct Thermal Degradation?
- Selection of an elastomer with improved thermal stability.
- Evaluation of the possibility of cooling surfaces
Explosive Decompression

What is Explosive Decompression?
The seal exhibits blisters, pits or pocks on its surface. Absorption of gas at high pressure and the subsequent rapid decrease in pressure. The absorbed gas blisters and ruptures the elastomer surface as the pressure is rapidly removed.
What causes Explosive Decompression? Condition such as:
- Rapid pressure changes
- Low-modulus hardness elastomer
How to correct Explosive Decompression?
- Higher-modulus/hardness elastomer
- Slower decompression (release of pressure)
Plasma Degradation
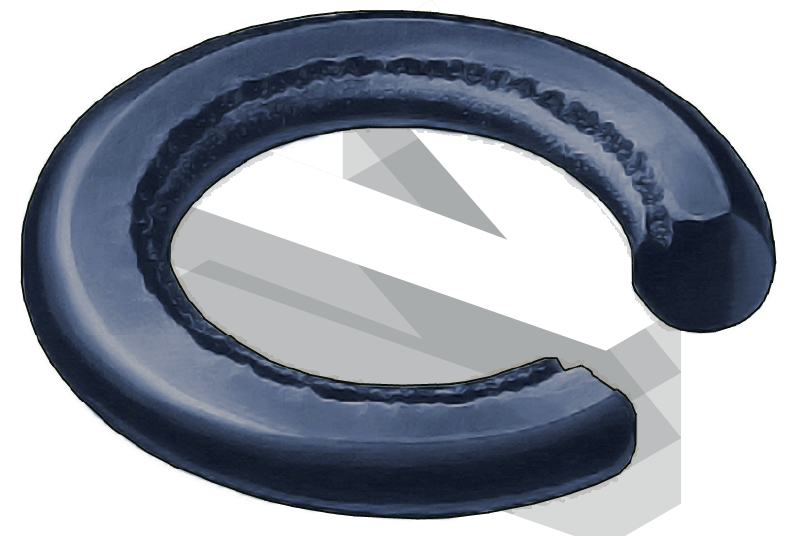
What is Plasma Degradation?
The seal often exhibits discolouration, as well as powdered residue on the surface and possible erosion of elastomer in the exposed area.
What causes Plasma Degradation? Condition such as:
- Chemical reactivity of the plasma.
- Ion bombardment (sputtering).
- Electron bombardment (heating).
- Improper gland design.
- Incompatible seal material.
How to correct Plasma Degradation?
- Plasma compatible elastomer and compound.
- Minimize exposed area.
- Examine gland design.
Contamination

What is Contamination?
The seal exhibits foreign materials on the surface and/or within the O-Ring.
What causes Contamination? Condition such as:
- Process environment deposition.
- Reactions or degradation of the elastomer.
- Non-semiconductor grade elastomer.
How to correct Contamination?
- Specify contamination level including manufacturing and packaging of the seals
Abrasion
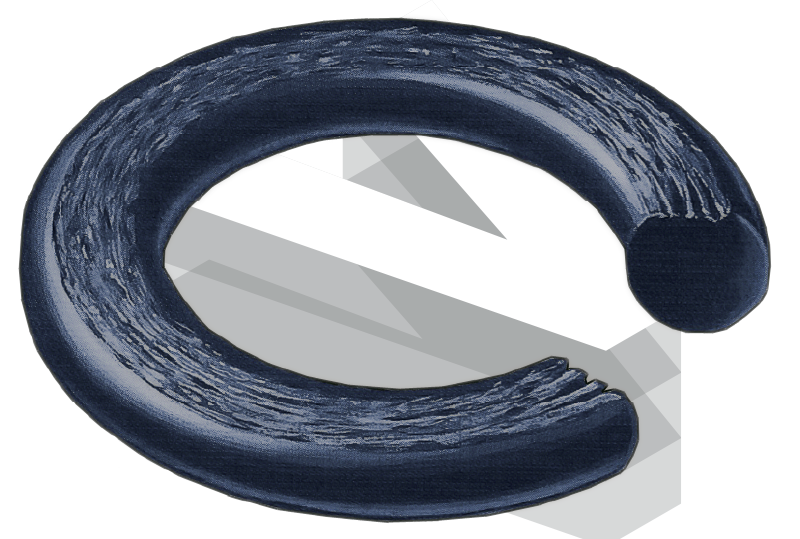
What is Abrasion?
The seal or parts of the seal exhibit a flat surface parallel to the direction or motion. Loose particles and scrapes may be found on the seal surface.
What causes Abrasion? Condition such as:
- Rough sealing surfaces.
- Excessive temperature.
- Process environment containing abrasive particles.
- Dynamic motion.
- Poor elastomer surface finish.
How to correct Abrasion?
- Use recommended gland surface finishes.
- Consider internally lubed eslastomers.
- Eliminate abrasive components.